www.usa-automation.net
01
'22
Written on Modified on
dSPACE News
Dspace provides solutions for developing and testing power electronics controllers for industrial applications
Our solutions support you in developing and testing power electronics controllers for industrial applications, such as production machines, power plant generators, robotics, and transportation. Typical applications include active front ends (AFE) that supply the common DC bus of the drive system and connect it bidirectionally to the power grid, and high-performance drives with high switching frequencies.
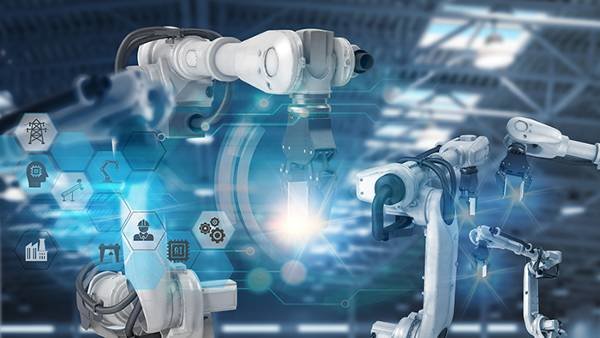
Challenges
Electric motors for industrial drive applications come in many different variants. Depending on the application, they differ in size and precision as well as in the drive power to be provided. In addition to the electric motor, industrial electric drives typically include inverters and rotary encoders, which also exist in numerous variants. Developing control algorithms for these machines is becoming increasingly complex for several reasons: Ever more fast-switching components are being used, regenerative capability is required, and parallel as well as interleaved structures are being used. The testing effort on the way to market maturity is also considerable for these machines, as the various possible combinations must be tested extensively in advance. However, since it is not possible to set up every combination in the real world, virtualization is key for efficient testing. In addition to the increased test coverage, virtualization also allows manufacturers to easily reproduce their tests and to test all kinds of situations, including those that might be too dangerous to test in the real world.
When testing very large or difficult-to-maintain systems, less relevant functions can be represented by digital twins.
Another important approach in the development and testing of industrial drives is the use of digital twins. Their integration into the test setup facilitates the simulation of entire systems instead of individual components, which is crucial when developing very large systems, such as printing machines, with hundreds of electric drives or systems that are difficult to maintain like wind power generators or large mining equipment. For testing, less relevant functions of these systems can be represented by digital twins.
dSPACE Solution
dSPACE has years of experience in meeting the special requirements of electric drives, which makes us a highly flexible and reliable partner, offering the most comprehensive solution portfolio for e-drive development and validation. You can use our cutting-edge hardware and software solutions for a wide range of industrial applications – from production machines and power plant generators to robotics and transportation. Benefit from the many advantages of our powerful FPGA-based hardware solutions, including:
- The fastest simulation platform on the market
- I/O interfaces with low latencies
- Interface gate drivers
- High-speed voltage, current, and position sensors
We also provide preconfigured models for a wide range of electric components. With ASM Electric Components, we offer real-time models for electric drive simulation. Our dSPACE XSG Electric Component Models allow for FPGA-based simulation of electric components that require high dynamics and precision. With our Electrical Power Systems Simulation (EPSS) Package, you can easily simulate power electronics circuits developed with Simscape Electrical™ (Specialized Power Systems) in real time.
Our dSPACE Engineering Services can give you turn-key solutions tailored to your individual requirements for a wide range of systems – from individual actuators to complete production machines.
www.dspace.com
Our dSPACE Engineering Services can give you turn-key solutions tailored to your individual requirements for a wide range of systems – from individual actuators to complete production machines.
www.dspace.com